JOIN OUR MAILING LIST |
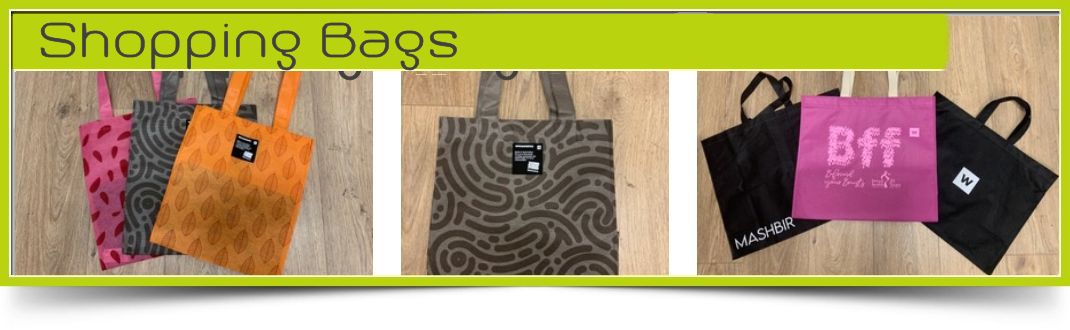
INTRODUCTION LETTER
I have travelled Africa on many occasions and what sticks out to me is the pollution. Roads are riddled with plastics. In S.A. we adopted the government policy to start imposing laws regarding shopping bags. When shopping you would now be charged for your plastics shopping bags that was prior to that for free. We also introduced an alternative of a reusable shopping bag that funny enough is also made of plastic. The product that goes into these bags are mostly recycled plastic waste. It is my intension to address this at an environment level in each African country. My intension is to export the wide with cloth in different plain dyed colours and printed designs. This will create job opportunities. We could also manufacture it locally if needed. With the prints we can also except logos for those shopping centres that want to brand their name.
The advantage of these shopping bags is that they can be reused over and over again. Once you have them not only can it be reused for the shopping trip, but also to transport other products from point A to B. With the logo prints there is also the advertising that is coupled to it. These bags currently are for sale in major stores especially those that used plastic bags
At the bottom there are clear photos from the point where these Plastic Bags and Plastic Bottles are collected by the Informal Sector and Collectors, Recycled Waste Removal Companies and in so creating work. These products are then washed and cleaned before it goes into a grinding process in order to finally come out as chips and flakes. These are then extruded and made into filament. These filaments are then stretched and cut, eventually becoming fibre. These fibres are pressed into bales and the final product is Stitch-bonded fabrics. The fabric then goes through dyeing and ends up in various forms, Mattress Ticking, Shopping Bags, Vertical Blinds, Waterproofing Material and a few other applications.
Also, quite imported that these fabrics are also coupled to Sewing, Ultra Sonic Welding, Printing, Embroidery, Coating and Laminating making them winners for a wide range of Markets.
It's "Made in S.A". and We Love It.
(In 2021 we used 54 Million Bottles worth of raw Material for StitchBond)
![]() |
![]() |
![]() |
![]() |
![]() |
![]() |
![]() |
![]() |
Manufactures a non-woven 100% polyester Stitchbond fabric at its plant in Cape
Town.
We are pleased with our ever-increasing role in the use of
rPET and thereby the reduction of single-use plastic.
We continue to develop products and markets with our
Stitchbonded fabrics made from rPET fibre.
In the 2021 calendar year we have consumed over 66 million
bottles worth of rPET fibre, based on the conversion factor
provided by Fibre Manufacturers, making a significant impact
in the reduction of plastic waste to landfill. And, this figure
grows year on year.
Several published studies consistently give top marks
to our Stitchbonded fabric made from rPET in terms of:
- Global Warming
- Land use
- Water use
- Affordability
Stitchbonding is a Textile Manufacturing process, resulting in a Non-Woven cloth suitable for a vast range of end uses.
Our rPet Stitchbonded fabrics are suitable for Sewing, Ultra-sonic welding, Printing, Dyeing, Embroidery, Coating, and Laminating, making them a winner for a wide range of markets.
Romatex manufactures its Stitchbonded fabrics locally, in Cape Town, and sources the vast majority of its raw material also locally. We provide an untold number of local companies with our range of fabrics, the resultant contribution to employment meaningful by any definition
The Recycling Process
Bottles are washed, rinsed and finally made into dried flakes as indicated below
- The flakes/chips are then extruded and made into a filament
- The filaments are then stretched and cut, eventually becoming fibre.
- The fibres are pressed into bales. These bales are delivered to Romatex where the fibres are processed into Stitchbonded fabric as well as a wider range of Home Textiles products.
Back | Back to top |